Canhão e Rosca para Injetora: Como Escolher e Manter Esses Componentes Essenciais
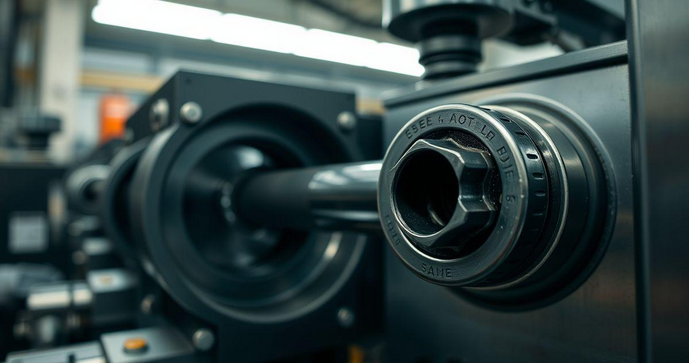
Por: João - 25 de Janeiro de 2025
O canhão e a rosca para injetora desempenham um papel crucial no processo de injeção plástica, influenciando diretamente a qualidade e a eficiência da produção. Compreender suas funções e características é essencial para otimizar o desempenho das injetoras e garantir resultados satisfatórios. Neste artigo, abordaremos a importância desses componentes, os diferentes tipos disponíveis no mercado e dicas valiosas para sua manutenção e escolha adequada.
Importância do Canhão e Rosca na Injeção Plástica
O canhão e a rosca são componentes fundamentais no processo de injeção plástica, desempenhando papéis essenciais que impactam diretamente a qualidade do produto final e a eficiência da operação. A compreensão da importância desses elementos é crucial para profissionais da indústria de plásticos, engenheiros e operadores de máquinas, pois a escolha e a manutenção adequadas podem resultar em melhorias significativas na produção.
O canhão é a parte do equipamento onde o material plástico é aquecido e fundido antes de ser injetado no molde. Sua função principal é garantir que o plástico atinja a temperatura ideal para a injeção, permitindo que o material flua de maneira uniforme e preencha todas as cavidades do molde. A eficiência do canhão está diretamente relacionada à sua capacidade de conduzir calor de forma eficaz, o que é essencial para evitar problemas como a degradação do material ou a formação de bolhas de ar.
A rosca, por sua vez, é responsável por transportar o material plástico fundido do canhão até a cavidade do molde. O design da rosca, incluindo seu comprimento, diâmetro e perfil, influencia a pressão e a velocidade do material durante a injeção. Uma rosca bem projetada pode otimizar o fluxo do plástico, reduzindo o tempo de ciclo e melhorando a qualidade do produto final. Além disso, a rosca deve ser capaz de lidar com diferentes tipos de materiais, desde plásticos de engenharia até compostos mais complexos.
Um dos principais benefícios de um canhão e rosca bem projetados é a redução de desperdícios. Quando o material é aquecido e transportado de maneira eficiente, há menos chances de que o plástico se degrade ou que ocorra a formação de resíduos. Isso não apenas economiza material, mas também reduz os custos operacionais e melhora a sustentabilidade do processo de produção.
Além disso, a escolha correta do canhão e da rosca pode impactar a qualidade do produto final. Um aquecimento inadequado pode resultar em produtos com falhas, como bolhas, manchas ou deformações. Por outro lado, um canhão e rosca que funcionam em harmonia garantem que o material seja injetado de forma consistente, resultando em peças com dimensões precisas e acabamentos de alta qualidade.
A manutenção regular do canhão e da rosca é igualmente importante. Com o tempo, o desgaste natural pode afetar a eficiência desses componentes, levando a problemas como vazamentos, variações na pressão de injeção e até mesmo falhas no equipamento. A implementação de práticas de manutenção preventiva, como a verificação de desgastes e a limpeza adequada, pode prolongar a vida útil do canhão e da rosca, além de garantir um desempenho consistente ao longo do tempo.
Outro aspecto a ser considerado é a compatibilidade dos materiais utilizados. Diferentes tipos de plásticos têm propriedades térmicas e mecânicas distintas, o que pode exigir ajustes no canhão e na rosca. Por exemplo, plásticos de alta viscosidade podem necessitar de uma rosca com um design específico para garantir um fluxo adequado. Portanto, é fundamental que os profissionais da indústria estejam cientes das características dos materiais que estão utilizando e como isso pode afetar a escolha do canhão e da rosca.
Além disso, a tecnologia tem avançado significativamente na área de injeção plástica, e novos materiais e designs de canhões e roscas estão sendo desenvolvidos para atender às demandas do mercado. Componentes como o ANEL DE BLOQUEIO são exemplos de inovações que podem melhorar a eficiência e a segurança do processo de injeção. Esses avanços tecnológicos não apenas aumentam a produtividade, mas também oferecem soluções para desafios específicos enfrentados na produção de plásticos.
Em resumo, a importância do canhão e da rosca na injeção plástica não pode ser subestimada. Esses componentes são essenciais para garantir a eficiência do processo, a qualidade do produto final e a sustentabilidade da operação. A escolha adequada, a manutenção regular e a adaptação às novas tecnologias são fatores que podem fazer a diferença entre uma produção bem-sucedida e uma cheia de desafios. Portanto, investir tempo e recursos na compreensão e otimização desses elementos é fundamental para qualquer profissional que atua na indústria de plásticos.
Tipos de Canhões e Roscas para Injetoras
Os canhões e roscas para injetoras são componentes cruciais que influenciam diretamente a eficiência e a qualidade do processo de injeção plástica. Existem diversos tipos de canhões e roscas disponíveis no mercado, cada um projetado para atender a necessidades específicas de produção e características dos materiais utilizados. Neste artigo, exploraremos os principais tipos de canhões e roscas, suas aplicações e como escolher o mais adequado para sua injetora.
Os canhões podem ser classificados de acordo com o material de construção, o design e a aplicação. Um dos tipos mais comuns é o canhão de aço, que oferece alta resistência e durabilidade. Este tipo é ideal para aplicações que exigem alta pressão e temperaturas elevadas, como a injeção de plásticos de engenharia. Além disso, os canhões de aço podem ser tratados termicamente para aumentar ainda mais sua resistência ao desgaste.
Outro tipo de canhão é o canhão de alumínio, que é mais leve e possui uma excelente condução térmica. Este tipo é frequentemente utilizado em aplicações que exigem aquecimento rápido e eficiente, como a injeção de plásticos de baixa viscosidade. No entanto, os canhões de alumínio podem não ser tão duráveis quanto os de aço, especialmente em condições de alta pressão.
Além dos materiais, o design do canhão também pode variar. Existem canhões de design simples, que são adequados para aplicações gerais, e canhões de design complexo, que possuem características específicas para otimizar o fluxo do material. Por exemplo, canhões com geometrias otimizadas podem melhorar a homogeneização do material, resultando em uma mistura mais uniforme e, consequentemente, em produtos de melhor qualidade.
Em relação às roscas, elas também podem ser classificadas de acordo com o seu design e aplicação. As roscas de passo largo são projetadas para transportar materiais de alta viscosidade, permitindo um fluxo mais eficiente. Esse tipo de rosca é ideal para plásticos que exigem uma maior pressão de injeção, como os plásticos de engenharia. Por outro lado, as roscas de passo fino são mais adequadas para materiais de baixa viscosidade, proporcionando um controle mais preciso do fluxo do material.
Outro aspecto importante a considerar ao escolher uma rosca é o seu perfil. Existem roscas com perfis diferentes, como roscas de seção circular, trapezoidal e quadrada. Cada perfil tem suas próprias características de desempenho e é adequado para diferentes tipos de materiais. Por exemplo, roscas com perfil trapezoidal são frequentemente utilizadas em aplicações que exigem um bom equilíbrio entre a capacidade de transporte e a homogeneização do material.
Além disso, as roscas podem ser projetadas para atender a requisitos específicos de produção. Por exemplo, algumas roscas são projetadas para permitir a injeção de materiais reciclados, enquanto outras são otimizadas para a injeção de compostos com aditivos especiais. A escolha da rosca certa pode impactar significativamente a eficiência do processo e a qualidade do produto final.
É importante mencionar que a manutenção adequada dos canhões e roscas é fundamental para garantir seu desempenho ideal. Com o tempo, o desgaste natural pode afetar a eficiência desses componentes, levando a problemas como vazamentos e variações na pressão de injeção. A implementação de práticas de manutenção preventiva, como a verificação de desgastes e a limpeza adequada, pode prolongar a vida útil do canhão e da rosca, além de garantir um desempenho consistente ao longo do tempo.
Além disso, a tecnologia tem avançado significativamente na área de injeção plástica, e novos materiais e designs de canhões e roscas estão sendo desenvolvidos para atender às demandas do mercado. Componentes como a Usinagem pesada são exemplos de inovações que podem melhorar a eficiência e a segurança do processo de injeção. Esses avanços tecnológicos não apenas aumentam a produtividade, mas também oferecem soluções para desafios específicos enfrentados na produção de plásticos.
Em resumo, a escolha do tipo de canhão e rosca para injetoras deve ser feita com base nas características do material a ser injetado, nas exigências do processo e nas especificações do produto final. Compreender as diferenças entre os tipos de canhões e roscas disponíveis no mercado é essencial para otimizar a produção e garantir a qualidade dos produtos. Investir na escolha certa e na manutenção adequada desses componentes é fundamental para o sucesso na indústria de injeção plástica.
Dicas para Manutenção de Canhão e Rosca
A manutenção adequada do canhão e da rosca é essencial para garantir o desempenho eficiente e a longevidade desses componentes na injeção plástica. A falta de cuidados pode levar a problemas sérios, como falhas no equipamento, redução da qualidade do produto final e aumento dos custos operacionais. Neste artigo, apresentaremos dicas valiosas para a manutenção de canhões e roscas, ajudando a maximizar a eficiência do seu processo de injeção.
Uma das primeiras etapas na manutenção do canhão e da rosca é a limpeza regular. O acúmulo de resíduos plásticos, poeira e sujeira pode afetar o desempenho do equipamento. É recomendável realizar uma limpeza visual após cada ciclo de produção, removendo detritos que possam ter se acumulado. Utilize um pano seco e evite o uso de água ou solventes que possam danificar os componentes elétricos e mecânicos.
Além da limpeza, a lubrificação é um aspecto crucial da manutenção. As partes móveis do canhão e da rosca devem ser lubrificadas regularmente para evitar o desgaste prematuro e garantir um funcionamento suave. Aplique um lubrificante adequado nos pontos recomendados pelo fabricante, geralmente em áreas como engrenagens e articulações. A frequência da lubrificação pode variar, mas uma aplicação a cada seis meses é uma boa prática, dependendo da intensidade de uso do equipamento.
Outro ponto importante a ser considerado é a verificação das conexões elétricas e mecânicas. Certifique-se de que todas as conexões estão firmes e que não há sinais de desgaste ou corrosão. Fios soltos podem causar falhas de funcionamento e até mesmo curtos-circuitos. Se você perceber qualquer sinal de dano nos cabos ou em componentes do sistema elétrico, é recomendável substituí-los imediatamente para evitar problemas futuros.
A inspeção regular do canhão e da rosca é fundamental para identificar desgastes e problemas antes que se tornem críticos. Realize uma verificação trimestral mais abrangente, observando todas as partes do motor e do portão em busca de desgaste, incluindo as dobradiças, os trilhos e as rodinhas. Certifique-se de que estão em bom estado e que não há sinais de corrosão. Verifique também se o portão está nivelado e se o motor opera sem ruídos anormais e sem falhas, o que pode indicar um problema.
Além disso, a calibração do canhão e da rosca deve ser realizada periodicamente. Isso envolve ajustar as configurações do equipamento para garantir que ele esteja operando nas condições ideais. Verifique a temperatura de operação, a pressão de injeção e a velocidade de rotação da rosca. Essas variáveis podem afetar diretamente a qualidade do produto final e a eficiência do processo. Consulte o manual do fabricante para obter orientações sobre como realizar esses ajustes corretamente.
É importante também monitorar a temperatura do canhão durante a operação. Temperaturas inadequadas podem levar à degradação do material plástico e à formação de bolhas de ar, resultando em produtos de baixa qualidade. Utilize termômetros e sensores para garantir que a temperatura esteja dentro da faixa recomendada pelo fabricante. Caso identifique variações significativas, verifique o sistema de aquecimento e faça os ajustes necessários.
Outro aspecto a ser considerado é a compatibilidade dos materiais utilizados. Diferentes tipos de plásticos têm propriedades térmicas e mecânicas distintas, o que pode exigir ajustes no canhão e na rosca. Por exemplo, plásticos de alta viscosidade podem necessitar de uma rosca com um design específico para garantir um fluxo adequado. Portanto, é fundamental que os profissionais da indústria estejam cientes das características dos materiais que estão utilizando e como isso pode afetar a escolha do canhão e da rosca.
Além disso, a tecnologia tem avançado significativamente na área de injeção plástica, e novos materiais e designs de canhões e roscas estão sendo desenvolvidos para atender às demandas do mercado. Componentes como a Usinagem de Cilindros são exemplos de inovações que podem melhorar a eficiência e a segurança do processo de injeção. Esses avanços tecnológicos não apenas aumentam a produtividade, mas também oferecem soluções para desafios específicos enfrentados na produção de plásticos.
Por fim, é recomendável manter um contato regular com um profissional qualificado para inspeções periódicas dos canhões e roscas. Técnicos podem identificar problemas precocemente durante a análise e oferecer soluções que evitem falhas maiores no futuro. Ao realizar inspeções regulares, você garantirá que o canhão e a rosca estejam em funcionamento adequado e atualizados com as tecnologias disponíveis.
Em resumo, a manutenção de canhões e roscas é um aspecto vital para garantir a eficiência e a qualidade do processo de injeção plástica. A limpeza regular, a lubrificação, a verificação das conexões, a calibração e a monitorização da temperatura são práticas essenciais que devem ser seguidas. Investir tempo e recursos na manutenção adequada desses componentes é fundamental para o sucesso na indústria de injeção plástica.
Como Escolher o Canhão e Rosca Ideais para Sua Injetora
Escolher o canhão e a rosca ideais para sua injetora é uma decisão crucial que pode impactar diretamente a eficiência do processo de injeção plástica e a qualidade do produto final. Com uma variedade de opções disponíveis no mercado, é fundamental entender as características e especificações de cada componente para fazer a escolha certa. Neste artigo, abordaremos os principais fatores a serem considerados ao selecionar o canhão e a rosca para sua injetora.
O primeiro passo na escolha do canhão e da rosca é entender as características do material que será injetado. Diferentes plásticos possuem propriedades térmicas e mecânicas distintas, o que pode exigir ajustes específicos no canhão e na rosca. Por exemplo, plásticos de alta viscosidade podem necessitar de um canhão e rosca projetados para suportar pressões mais elevadas e garantir um fluxo adequado. Portanto, é essencial conhecer as especificações do material e como ele se comporta durante o processo de injeção.
Outro fator importante a ser considerado é a temperatura de processamento do material. O canhão deve ser capaz de aquecer o plástico a uma temperatura ideal para garantir que ele se torne maleável e flua corretamente. A escolha de um canhão com um sistema de aquecimento eficiente é fundamental para evitar problemas como a degradação do material ou a formação de bolhas de ar. Além disso, a rosca deve ser projetada para manter a temperatura adequada durante o transporte do material até o molde.
O design da rosca também desempenha um papel crucial na escolha do canhão e da rosca ideais. Existem diferentes perfis de rosca, como roscas de passo largo e passo fino, cada uma adequada para diferentes tipos de materiais e aplicações. As roscas de passo largo são mais indicadas para plásticos de alta viscosidade, enquanto as de passo fino são mais adequadas para materiais de baixa viscosidade. A escolha do perfil correto pode otimizar o fluxo do material e melhorar a qualidade do produto final.
Além disso, a capacidade de transporte da rosca deve ser considerada. A rosca deve ser capaz de mover o material de forma eficiente do canhão até a cavidade do molde, garantindo que o plástico seja injetado de maneira uniforme. Um design de rosca inadequado pode resultar em problemas como a formação de bolhas, variações na pressão de injeção e até mesmo falhas no produto final. Portanto, é importante escolher uma rosca que atenda às necessidades específicas do seu processo de injeção.
Outro aspecto a ser considerado é a durabilidade dos componentes. O canhão e a rosca estão sujeitos a desgaste ao longo do tempo, especialmente em aplicações de alta demanda. Portanto, é fundamental escolher materiais de alta qualidade que ofereçam resistência ao desgaste e à corrosão. Canhões e roscas feitos de aço tratado termicamente, por exemplo, tendem a ter uma vida útil mais longa e a manter seu desempenho ao longo do tempo.
A manutenção também deve ser levada em conta ao escolher o canhão e a rosca. Componentes que exigem manutenção frequente podem aumentar os custos operacionais e o tempo de inatividade da máquina. Portanto, é recomendável optar por canhões e roscas que sejam projetados para facilitar a manutenção, com acesso fácil a partes que precisam ser limpas ou lubrificadas. Isso não apenas economiza tempo, mas também garante que o equipamento funcione de maneira eficiente.
Além disso, a tecnologia tem avançado significativamente na área de injeção plástica, e novos designs de canhões e roscas estão sendo desenvolvidos para atender às demandas do mercado. Componentes como a usinagem de roscas são exemplos de inovações que podem melhorar a eficiência e a segurança do processo de injeção. Esses avanços tecnológicos não apenas aumentam a produtividade, mas também oferecem soluções para desafios específicos enfrentados na produção de plásticos.
Por fim, é sempre recomendável consultar especialistas ou fornecedores de equipamentos de injeção plástica ao escolher o canhão e a rosca ideais. Profissionais experientes podem oferecer orientações valiosas com base em suas necessidades específicas e nas características do material que você está utilizando. Além disso, eles podem ajudar a identificar as melhores opções disponíveis no mercado, garantindo que você faça a escolha certa para sua injetora.
Em resumo, a escolha do canhão e da rosca ideais para sua injetora envolve considerar as características do material, a temperatura de processamento, o design da rosca, a durabilidade dos componentes e a facilidade de manutenção. Investir tempo na seleção adequada desses elementos é fundamental para otimizar o processo de injeção plástica e garantir a qualidade do produto final. Com as informações corretas e o suporte de especialistas, você estará bem preparado para fazer a escolha certa e maximizar a eficiência da sua operação.
Em conclusão, a escolha e a manutenção adequadas do canhão e da rosca para injetora são fundamentais para garantir a eficiência e a qualidade no processo de injeção plástica. Compreender as características dos materiais, as especificações dos componentes e as melhores práticas de manutenção pode resultar em uma produção mais eficiente e em produtos finais de alta qualidade. Ao investir tempo e recursos na seleção correta e na manutenção regular desses elementos, você estará contribuindo para o sucesso da sua operação e para a satisfação dos seus clientes.