Rosca para Extrusora: Como Escolher a Ideal
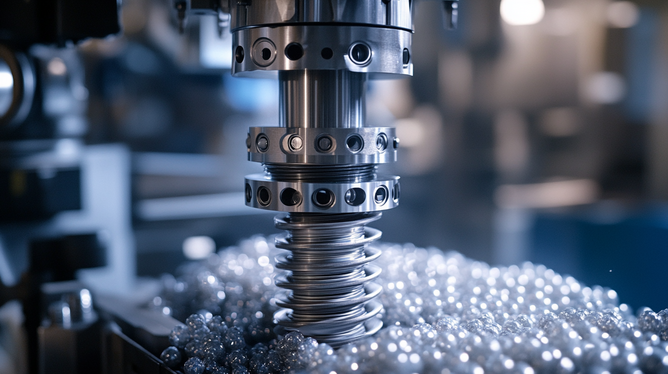
Por: João - 07 de Dezembro de 2024
A rosca para extrusora é um componente fundamental na indústria de transformação de plásticos e outros materiais. Ter conhecimento sobre suas características e aplicações pode fazer toda a diferença na eficiência do processo produtivo. Neste artigo, vamos explorar os diferentes tipos de rosca para extrusora, suas vantagens e como escolher a opção mais adequada para suas necessidades. Continue lendo e descubra como otimizar sua produção com a rosca ideal!
Tipos de Rosca para Extrusora
A rosca para extrusora desempenha um papel crucial na transformação dos materiais, especialmente na indústria de plásticos. Existem vários tipos de roscas, cada uma com suas específicas aplicações e características. Compreender essas variações ajuda na escolha do tipo ideal para processos industriais. A seguir, vamos explorar os principais tipos de roscas para extrusora com mais detalhes.
Rosca Simples
A rosca simples é um dos tipos mais comuns utilizados na extrusão de plásticos. Este tipo possui uma única hélice que se estende ao longo da barra de extrusão. É geralmente mais fácil de fabricar e tem um custo mais baixo em comparação com outros tipos de roscas. A rosca simples é indicada para materiais de baixo peso molecular, pois proporciona uma mistura e aquecimento adequados durante o processo de extrusão.
Como a rosca é composta por apenas uma hélice, ela tende a ter um fluxo mais uniforme de material, o que é benéfico para muitos processos. No entanto, seu desempenho pode ser limitado quando se trata de materiais mais viscosos ou de alta densidade. Para esses materiais, a rosca simples pode não ser a melhor opção.
Rosca Dupla
A rosca dupla é um avanço em relação à rosca simples, pois possui duas hélices que operam em paralelo. Este design permite uma mistura mais eficiente e um aquecimento mais homogêneo do material durante a extrusão. É ideal para processar materiais de alta viscosidade e garantir uma melhor homogeneização.
Existem diferentes configurações de roscas duplas, como as co-rotativas e contra-rotativas. As roscas co-rotativas giram na mesma direção, enquanto as contra-rotativas giram em direções opostas. Ambas as configurações têm suas vantagens, sendo as co-rotativas mais comuns. Elas permitem maior interação entre o material e a rosca, o que resulta em uma mistura mais eficiente.
As roscas duplas também são altamente versáteis e podem ser utilizadas em uma ampla gama de aplicações, incluindo a produção de compostos plásticos e reciclados, além de ajudar na desidratação de produtos. A combinação de eficiência e flexibilidade torna este tipo de rosca uma escolha popular para muitas operações de extrusão.
Rosca Tripoidal
A rosca tripoidal, também conhecida como rosca de três vias, é um tipo menos comum, mas oferece vantagens significativas em aplicações específicas. Esse design possui três hélices que se entrelaçam, permitindo uma mistura ainda mais eficaz. A rosca tripoidal é ideal para aplicações que exigem alta taxa de mistura e homogeneização, como, por exemplo, a produção de compostos que incorporam aditivos químicos e pigmentos.
Outra vantagem da rosca tripoidal é que ela pode proporcionar uma maior capacidade de transporte de material. Isso significa que, em algumas operações, uma rosca tripoidal pode ser mais eficiente do que as roscas simples ou duplas, especialmente quando se lidam com materiais altamente viscosos.
No entanto, a rosca tripoidal é mais complexa de fabricar e pode ter um custo mais elevado. Além disso, a sua aplicação deve ser considerada com cuidado, pois não é necessariamente a melhor opção para todas as operações de extrusão.
Rosca de Alta Torque
A rosca de alta torque é projetada para lidar com materiais que requerem uma força maior durante o processo de extrusão. Esse tipo de rosca é muitas vezes utilizada em aplicações industriais que envolvem a extrusão de polímeros de alta viscosidade ou que contenham aditivos que aumentam a resistência do material. A rosca de alta torque é caracterizada por um design mais robusto, que pode suportar os esforços mecânicos elevados durante a operação.
A escolha de usar uma rosca de alta torque depende principalmente das características do material a ser processado. Além disso, a configuração de torque elevado pode ajudar a evitar problemas como a degradação do material ou a formação de bolhas durante o processo de extrusão.
Rosca Segmentada
A rosca segmentada é uma solução inovadora que se destaca pela sua flexibilidade e customização. Esse tipo de rosca é composta por seções, ou segmentos, que podem ser trocados ou ajustados conforme as necessidades das operações de extrusão. Este tipo de rosca se adapta a diferentes aplicações, permitindo que os fabricantes personalizem suas extrusoras para processar uma ampla gama de materiais.
A rosca segmentada permite não apenas a configuração do design da hélice, mas também a alteração do passo e do diâmetro da rosca, conforme necessário. Isso proporciona a possibilidade de otimizar o processo de extrusão em tempo real, levando a uma maior eficiência e menores custos operacionais.
Rosca de Síncope
As roscas de síncope são um tipo especializado de rosca projetada para extrusão de materiais com alta sensibilidade à temperatura. O design desse tipo de rosca ajuda a minimizar a geração de calor, o que é essencial para evitar a degradação do material. A rosca de síncope é frequentemente empregada em aplicações que envolvem a extrusão de polímeros que podem ser afetados negativamente por altas temperaturas.
Um ponto a destacar sobre a rosca de síncope é que ela pode ajudar a manter a estabilidade térmica do processo, resultando em produtos de alta qualidade e consistência. Assim, essa rosca é uma excelente escolha para quem trabalha com materiais delicados e precisa de controle rigoroso sobre as condições do processo de extrusão.
Considerações Finais sobre os Tipos de Rosca
Ao escolher o tipo de rosca para extrusora ideal, é vital considerar diversos fatores, como o tipo de material a ser processado, as características específicas do produto final e os requisitos do processo. É sempre recomendável consultar especialistas no assunto e realizar testes para determinar qual rosca trará os melhores resultados em cada situação.
Ademais, o avanço tecnológico na indústria de extrusão continua a produzir inovações. À medida que novas aplicações e materiais emergem, novos tipos de roscas são desenvolvidos para atender a essas demandas. Portanto, estar bem informado sobre os diferentes tipos de rosca disponíveis no mercado pode garantir que você esteja sempre preparado para as mudanças e tendências do setor.
Por fim, escolha sabiamente a rosca para extrusora, pois ela pode impactar tanto na eficiência do seu processo industrial quanto na qualidade dos produtos que você produz.
Vantagens da Rosca para Extrusora Ideal
A escolha da rosca para extrusora correta pode ter um impacto significativo na eficiência e qualidade do processo de extrusão. É essencial entender as vantagens que a rosca ideal pode trazer para a produção, pois isso pode melhorar a performance dos equipamentos e a qualidade do produto final. Neste artigo, vamos explorar em detalhes as principais vantagens de uma rosca para extrusora que se adapta perfeitamente às suas necessidades.
Otimização do Processo de Extrusão
Uma rosca para extrusora ideal é projetada especificamente para otimizar o processo de extrusão. Isso significa que ela facilita um transporte eficiente do material através do cilindro, minimizando a retenção e os pontos de bloqueio. Com a rosca adequada, é possível melhorar a taxa de produção, mantendo a qualidade do material extrudado.
Além disso, a eficiência térmica da rosca ideal reduz o tempo de aquecimento do material, o que pode resultar em menor consumo de energia. Isso significa que a empresa pode operar a extrusora com menor custo e maior produção, uma combinação que é excelente para a competitividade no mercado.
Aumento na Qualidade do Produto Final
A qualidade do produto final é de extrema importância em qualquer processo de extrusão. A rosca adequada contribui para um melhor controle da temperatura e do tempo de residência do material. Isso minimiza a degradação dos polímeros e assegura que as propriedades desejáveis sejam mantidas.
Dessa forma, o produto final terá características mecânicas superiores, como resistência e durabilidade. Além disso, uma boa rosca ajuda a evitar problemas como bolhas ou falhas na estrutura e homogeneidade do produto extrudado, garantindo que a qualidade atenda aos padrões exigidos pelo mercado.
Versatilidade na Aplicação de Materiais
A rosca para extrusora ideal oferece versatilidade na aplicação de diferentes tipos de materiais. Existem roscas projetadas para processar não apenas plásticos, mas também compósitos, borrachas e até mesmo materiais reciclados. Essa versatilidade é especialmente importante para empresas que trabalham com uma variedade de produtos e precisam de equipamentos que possam ser adaptados.
Além disso, algumas roscas permitem uma melhor capacidade de mistura, facilitando a incorporação de aditivos, pigmentos e outros componentes. Isso é fundamental para garantir que o produto final tenha as propriedades desejadas e que o processo de produção seja eficiente.
Redução de Desperdício e Resíduos
Uma rosca para extrusora ideal pode contribuir significativamente para a redução de desperdício e resíduos durante o processo de produção. Com um design que minimiza a retenção de material dentro da máquina, é possível extrudar uma maior quantidade do material que entra na linha de produção.
Adicionalmente, uma rosca que opera eficientemente evita a má mistura de materiais e a formação de produtos defeituosos. Isso gera uma redução nos resíduos gerados, resultando em menos perda de material e menores custos de descarte. Assim, as empresas se tornam mais sustentáveis e eficientes em seus processos.
Facilidade de Manutenção
Uma rosca para extrusora ideal é projetada para facilitar a manutenção, o que é um aspecto importante para a operação contínua do equipamento. Roscas que são fabricadas com materiais de alta resistência tendem a ser mais duráveis e necessitam de menos manutenção ao longo do tempo.
Quando a manutenção é necessária, a rosca ideal pode ser projetada para permitir uma desmontagem e montagem rápida, o que minimiza o tempo de inatividade da máquina. Isso é especialmente importante em ambientes industriais onde o tempo de produção é valioso e o equipamento precisa operar de maneira contínua.
Aumento da Eficiência Energética
Uma das grandes vantagens da rosca para extrusora ideal é a sua capacidade de aumentar a eficiência energética do processo de extrusão. Quando uma rosca é projetada para otimizar o fluxo e o aquecimento do material, ela consome menos energia durante a operação. Essa economia de energia não apenas reduz os custos operacionais, mas também colabora para práticas de produção mais sustentáveis.
A eficiência energética é um fator de grande importância, especialmente com o aumento dos custos de energia e a conscientização sobre a sustentabilidade. Uma rosca que consome menos energia contribui para a responsabilidade ambiental da empresa e pode até mesmo gerar economia significativa no longo prazo.
Integração com Tecnologias Avançadas
As roscas para extrusora mais recentes podem ser integradas a tecnologias avançadas, como sistemas de controle automatizados e monitoramento em tempo real. Esta integração proporciona um controle muito mais preciso durante o processo de extrusão, permitindo ajustes dinâmicos e otimização contínua.
Além disso, a capacidade de monitorar e ajustar parâmetros como temperatura, pressão e velocidade em tempo real assegura que a produção esteja sempre em seu nível ideal de eficiência. Isso minimiza problemas e permite que as empresas se mantenham competitivas em um mercado em constante evolução.
Facilidade em Processos de Reciclagem
A rosca para extrusora ideal pode ser uma grande aliada em processos de reciclagem. Com o aumento da demanda por produtos sustentáveis, muitas empresas estão se voltando para a reciclagem de plásticos. Uma rosca bem projetada permite a extrusão eficiente de materiais reciclados, garantindo que as propriedades dos materiais sejam mantidas durante todo o processo.
A utilização de roscas que suportam a reciclagem não apenas contribui para práticas sustentáveis, mas também pode ajudar a reduzir custos. Em vez de depender exclusivamente de materiais virgens, as empresas podem reaproveitar resíduos e retornar materiais para a linha de produção, beneficiando o meio ambiente e a saúde financeira da empresa.
Impacto Positivo na Produção em Larga Escala
Para empresas que operam em grande escala, a rosca para extrusora ideal é um fator determinante para o sucesso da produção. A eficiência, a versatilidade e a qualidade resultante do uso de uma rosca adequada se traduzem em volumes de produção mais elevados sem comprometer a qualidade do produto. Isso é essencial para atender à demanda do mercado e permanecer competitivos.
Além disso, a confiabilidade e a durabilidade de uma boa rosca garantem que os equipamentos não apresentem falhas frequentes, permitindo que a produção ocorra de maneira contínua. Isso é um aspecto vital para empresas que dependem de grandes quantidades de produto e que não podem se dar ao luxo de parar a produção regularmente para manutenção ou recuperação de falhas.
Considerações Finais Sobre a Escolha da Rosca Ideal
Em suma, as vantagens de se escolher a rosca para extrusora ideal são inúmeras e se refletem em todos os aspectos do processo de extrusão, desde a eficiência na produção até a qualidade do produto final.
É importante que as empresas considerem cuidadosamente as suas necessidades específicas antes de decidir qual tipo de rosca utilizar. As vantagens mencionadas mostram que uma boa escolha pode resultar em ganhos significativos em termos de qualidade, eficiência e economia de custos.
Assim, antes de finalizar a decisão, é sempre recomendável consultar especialistas e realizar testes quando necessário. Isso garantirá que a rosca escolhida se alinhe perfeitamente ao processo de produção e às metas da empresa, resultando em um desempenho otimizado e na satisfação do cliente.
Como Escolher a Rosca Adequada
A escolha da rosca adequada para uma extrusora é uma decisão essencial para garantir que o processo de extrusão seja eficiente e que o produto final atenda aos requisitos de qualidade. Com a variedade de opções disponíveis no mercado, pode ser desafiador determinar qual rosca é a mais apropriada para suas necessidades específicas. Neste artigo, discutiremos em detalhe os fatores a serem considerados ao escolher a rosca para extrusora ideal, ajudando você a tomar uma decisão informada.
Entenda o Material a Ser Processado
Um dos primeiros passos na escolha da rosca correta é entender o tipo de material que será processado. O comportamento do material durante a extrusão varia conforme suas propriedades físicas e químicas, como viscosidade, temperatura de fusão e sensibilidade térmica.
Materiais com alta viscosidade, por exemplo, podem exigir roscas que proporcionem maior empuxo e mistura, enquanto materiais de baixo peso molecular podem ser mais adequados para roscas simples. Além disso, a presença de aditivos ou cargas também deve ser considerada, pois pode influenciar a escolha do design da rosca.
Aplique os Parâmetros do Processo
Os parâmetros do processo de extrusão, como temperatura, pressão e taxa de produção, também têm um papel crucial na escolha da rosca adequada. Cada tipo de rosca tem suas próprias características em relação à forma como interage com esses parâmetros.
Por exemplo, uma rosca projetada para alta pressão pode não funcionar eficientemente em um processo de baixa pressão, resultando em baixa produtividade e problemas de qualidade. Portanto, é essencial alinhar as especificações da rosca com os parâmetros operacionais esperados.
Considere o Design da Rosca
O design da rosca - incluindo o passo, diâmetro e forma da hélice - pode afetar significativamente o desempenho da extrusora. O passo da rosca refere-se à distância entre as hélices, enquanto o diâmetro influencia a capacidade de transporte e a eficiência de mistura.
A escolha do design da rosca deve ser feita com base na aplicação específica. Roscas de passo longo podem proporcionar um fluxo uniforme, enquanto roscas de passo curto podem ser mais eficazes em processos que exigem uma mistura intensa.
Identifique as Vantagens das Roscas Duplas
As roscas duplas têm ganhado popularidade devido às suas vantagens significativas em relação às roscas simples. Se você pretende processar materiais complexos ou deseja obter uma mistura mais homogênea, uma rosca dupla pode ser a melhor escolha.
As roscas duplas podem operar com maior eficiência, proporcionando um melhor controle térmico e mecânico, reduzindo a degradação do material e melhorando a qualidade do produto final. Portanto, se seus requisitos de extrusão incluem a necessidade de versatilidade e homogeneização aprimorada, opte por uma rosca dupla.
Considere a Capacidade de Transporte
A capacidade de transporte da rosca é relevante para garantir que o material flua adequadamente através da extrusora. A eficiência do transporte pode impactar diretamente a taxa de produção e a qualidade do produto final.
Para determinar a capacidade de transporte ideal, você deve considerar não apenas o design da rosca, mas também o material que está sendo processado. Materiais de alta viscosidade e densidade exigem roscas com maior empuxo e capacidade de transporte.
Avalie a Manutenção e Durabilidade
A manutenção e a durabilidade da rosca devem ser fatores-chave na sua escolha. Roscas que são feitas de materiais de alta resistência e que têm designs moduláveis podem reduzir os custos de manutenção ao longo do tempo.
Além disso, uma rosca com uma construção robusta não só prolonga a vida útil do equipamento, mas também minimiza o tempo de inatividade devido a quebras ou falhas. Escolher uma rosca que exija menos manutenção e que possa ser facilmente substituída pode ser benéfico para a eficiência operacional.
Adapte-se às Necessidades Específicas da Indústria
As diferentes indústrias têm requisitos específicos que podem influenciar a escolha da rosca. Por exemplo, na indústria alimentícia, a conformidade com padrões de saúde e segurança é fundamental, enquanto na indústria de plásticos, a eficiência e a velocidade de produção podem ser mais críticas.
Assim, adapte sua escolha de rosca para atender aos padrões e exigências específicas da sua indústria, considerando aspectos como a segurança dos produtos, as propriedades mecânicas desejadas e as certificações necessárias.
Eficiência Energética
A eficiência energética é uma consideração crescente na escolha de roscas para extrusoras. Roscas que são projetadas para operar com menor consumo de energia não só ajudam a reduzir custos operacionais, mas também contribuem para práticas industriais mais sustentáveis.
A escolha de uma rosca que minimize o consumo de energia e maximize a produção pode ter um impacto complexo no desempenho econômico da empresa. Portanto, analise as especificações energéticas do tipo de rosca que você considera e busque uma opção que alinhe eficiência energética e performance.
Consulta a Especialistas
Quando a escolha da rosca não parece clara, não hesite em consultar especialistas. Engenheiros e fabricantes de equipamentos de extrusão têm o conhecimento técnico necessário para ajudar a determinar a melhor opção para as suas necessidades específicas.
A consultoria especializada pode incluir análises de desempenho, simulações e testes em laboratório, garantindo que a rosca escolhida não apenas atenda aos requisitos do processo, mas também traga benefícios a longo prazo, como menor custo operacional e melhor qualidade do produto final.
Realização de Testes Práticos
Por fim, a realização de testes práticos pode ser uma maneira eficaz de garantir que você fez a escolha certa. Trabalhar com amostras de materiais e distintas configurações de roscas pode fornecer dados valiosos sobre o desempenho real de diferentes opções.
Esses testes podem reservar surpresas agradáveis, como descobrir que um tipo de rosca relativamente desconhecido pode ser a solução ideal para seu processo de produção. Assim, nunca subestime os benefícios de um experimento prático que envolva as roscas em questão.
Considerações Finais
Escolher a rosca adequada para extrusora é uma tarefa complexa que requer avaliação cuidadosa de diversos fatores. Compreender o material a ser processado, aplicar os parâmetros do processo, considerar o design da rosca e identificar a capacidade de transporte são etapas fundamentais para essa escolha.
Além disso, a manutenção, durabilidade e a adaptação às necessidades específicas da indústria são aspectos que devem ser levados em conta. Por fim, se possível, consulte especialistas e conduza testes práticos para fazer a escolha mais acertada e garantir o sucesso do seu processo de extrusão.
Manutenção da Rosca para Extrusora
A manutenção da rosca para extrusora é um aspecto crucial que pode impactar significativamente a eficiência do processo de extrusão, a qualidade do produto final e a longevidade do equipamento. Neste artigo, abordaremos as melhores práticas de manutenção, os tipos de problemas que podem ocorrer, bem como sinais de que a sua rosca pode precisar de atenção. Com essas informações, você estará melhor preparado para garantir que sua extrusora opere de maneira eficaz.
Importância da Manutenção da Rosca
A rosca para extrusora é um dos componentes mais críticos do processo de extrusão. Uma rosca bem mantida assegura que o material seja transportado, aquecido e misturado de forma adequada. A manutenção inadequada ou negligente pode levar a vários problemas, incluindo:
- Degradação do Material: Uma rosca suja ou danificada pode causar degradação dos polímeros, afetando as propriedades do produto final.
- Paradas Não Planejadas: Falhas mecânicas na rosca podem resultar em paradas inesperadas, afetando a produtividade e aumentando os custos operacionais.
- Desperdício de Material: Uma rosca com problemas pode resultar em maior desperdício de material, impactando diretamente nos custos.
- Inconsistência na Qualidade: A rosca danificada pode levar a variações na qualidade do produto final, prejudicando a reputação da empresa.
Tipos de Manutenção
Existem dois principais tipos de manutenção que devem ser considerados para a rosca da extrusora: a manutenção preventiva e a manutenção corretiva.
Manutenção PreventivaA manutenção preventiva envolve atividades programadas realizadas para evitar falhas e prolongar a vida útil do equipamento. Esta abordagem inclui:
- Inspeções Regulares: Verificar visualmente a rosca para identificar sinais de desgaste ou danos.
- Limpando a Rosca: Remover resíduos acumulados e sujeira que podem obstruir o fluxo de material.
- Lubrificação: Aplicar lubrificantes apropriados em partes móveis para garantir um funcionamento suave.
- Verificação de Alinhamento: Certificar-se de que a rosca está corretamente alinhada com os outros componentes para evitar desgaste irregular.
- Simulações de desempenho: Realizar testes em condições controladas para verificar o desempenho da rosca e identificar áreas de melhoria.
A manutenção corretiva, por sua vez, refere-se a ações tomadas para corrigir falhas que já ocorreram. Esse tipo de manutenção pode ser mais disruptivo e custoso, pois envolve a parada do equipamento e reparos. O ideal é evitar esse tipo de manutenção através de boas práticas da manutenção preventiva.
Sinais de Que a Rosca Precisa de Manutenção
Identificar os sinais de que a rosca precisa de manutenção é essencial para evitar falhas catastróficas. Aqui estão alguns dos sinais mais comuns:
- Ruídos Estranhos: Ruídos inesperados durante a operação podem indicar que algo está errado, como peças soltas ou desgastadas.
- Vibrações Excessivas: Vibrações que não são normais podem ser um sinal de problemas de alinhamento ou desgaste na rosca.
- Desempenho Irregular: Se a extrusora não estiver atingindo as taxas de produção esperadas, isso pode ser um indicativo de problemas com a rosca.
- Alterações na Qualidade do Produto: Se o produto final estiver apresentando falhas de qualidade, isso pode estar relacionado a uma rosca mal mantida.
Procedimentos de Limpeza
A limpeza regular da rosca é fundamental para manter a eficiência dela. Aqui estão algumas dicas para uma limpeza eficaz:
- Desmontagem: Em muitos casos, é necessário desmontar a rosca para uma limpeza completa. Siga as diretrizes do fabricante para remover a rosca de forma segura.
- Uso de Solventes: Utilize solventes adequados para remover resíduos plásticos e outros contaminantes que possam ter se acumulado na rosca.
- Escovação: Utilize escovas de cerdas macias para limpar as superfícies da rosca, evitando danos ao material.
- Inspeção Visual Durante a Limpeza: Aproveite a oportunidade para verificar a condição geral da rosca e procurar por sinais de desgaste ou danos.
Lubrificação
A lubrificação adequada é vital para o funcionamento suave da rosca na extrusora. Aqui estão algumas orientações sobre como realizar uma lubrificação eficaz:
- Escolha do Lubrificante: Utilize oleos ou graxas de acordo com as recomendações do fabricante da extrusora.
- Frequência de Lubrificação: A lubricação deve ser realizada regularmente, de acordo com o uso da extrusora e as recomendações do fabricante.
- Evite Excessos: A aplicação excessiva de lubrificante pode causar contaminação do produto final, portanto, siga as instruções cuidadosamente.
Inspeções Regulares
As inspeções regulares são uma parte fundamental da manutenção da rosca. Realizar inspeções sistemáticas permite identificar problemas potenciais antes que eles se tornem críticos. Aqui estão alguns aspectos a serem considerados ao realizar uma inspeção:
- Verifique a Rugosidade da Superfície: Utilize instrumentos de medição para avaliar o desgaste da superfície da rosca.
- Examine a Geometria da Rosca: Avalie se houve alterações na forma da rosca, que podem indicar problemas de desgaste ou danos.
- Cheque os Parafusos de Fixação: Verifique se todos os parafusos de fixação estão bem apertados para evitar vibrações.
Técnicas para Prevenir Desgaste Prematuro
Após estabelecer um plano de manutenção, é importante implementar técnicas para evitar o desgaste prematuro da rosca. Aqui estão algumas sugestões:
- Monitoramento da Temperatura: Controle a temperatura de operação da extrusora para evitar superaquecimento, que pode causar danos ao material.
- Controle do Fluxo de Material: Mantenha o fluxo de material dentro dos parâmetros recomendados para evitar sobrecargas na rosca.
- Treinamento da Equipe: Proporcione treinamento adequado para a equipe operadora, garantindo que todos saibam como operar o equipamento conforme as especificações.
- Ajustes Programados: Realize ajustes regulares e programados na configuração da extrusora conforme necessário para manter a eficiência.
Uso de Tecnologias para Monitoramento
Implementar tecnologias de monitoramento pode melhorar significantemente a manutenção da rosca para extrusora. Com o uso de sensores e sistemas automatizados, é possível monitorar continuamente o desempenho do equipamento. Algumas vantagens incluem:
- Detecção Precoce de Problemas: Sensores podem detectar falhas e enviar alertas antes que os problemas se tornem críticos.
- Dados em Tempo Real: Fornecimento de dados em tempo real sobre a operação da rosca, o que ajuda na tomada de decisões rápidas.
- Relatórios e Análises: Geração de relatórios permite análises detalhadas sobre o desempenho do equipamento, auxiliando na programação da manutenção.
Planejamento da Substituição da Rosca
Com o tempo, mesmo a rosca mais bem mantida pode precisar ser substituída. Portanto, é essencial ter um plano de substituição. Aqui estão alguns fatores a considerar:
- Vida Útil Estimada: Conheça a vida útil média da rosca e faça a substituição antes que ela atinja esse limite para evitar quebras.
- Condições Operacionais: Se a extrusora estiver operando em condições extremas, a rosca pode precisar ser substituída mais cedo.
- Avaliação Frequente: Realize avaliações frequentes para monitorar o desempenho da rosca e identificar quando a substituição se torna necessária.
Considerações Finais
Manter a rosca para extrusora em boas condições é fundamental para garantir a eficiência do processo de extrusão e a qualidade do produto final. As práticas de manutenção preventiva, a realização de inspeções regulares e a utilização de tecnologias de monitoramento são essenciais para evitar problemas e prolongar a vida útil do equipamento.
Além disso, ao conhecer os sinais de problemas e implementar estratégias para a manutenção, você poderá operar sua extrusora com confiança, reduzindo o tempo de inatividade e os custos operacionais. Em última análise, a manutenção eficaz da rosca para extrusora não só melhora o desempenho geral do equipamento, mas também pode contribuir para a rentabilidade da sua operação. Portanto, invista tempo e recursos em um programa de manutenção robusto e consistente.
Em resumo, a rosca para extrusora é um elemento crucial que desempenha um papel vital na eficiência e qualidade dos processos de extrusão. Compreender os diferentes tipos de roscas, suas características, vantagens e como escolher a opção adequada são passos essenciais para otimizar sua produção. Além disso, a manutenção adequada da rosca também é fundamental para garantir sua durabilidade e desempenho ao longo do tempo. Ao implementar as melhores práticas discutidas, você estará em condições de maximizar a eficiência de sua linha de produção, reduzir desperdícios e assegurar a qualidade do produto final. Invista no conhecimento sobre roscas para extrusoras e transforme seus processos produtivos em experiências de sucesso!