Rosca para extrusora de borracha: como escolher a ideal para sua produção
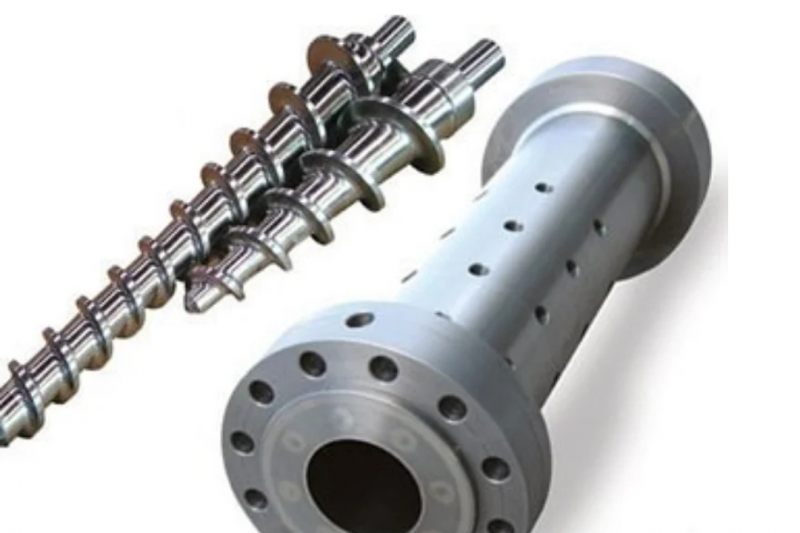
Por: João - 26 de Fevereiro de 2025
A rosca para extrusora de borracha desempenha um papel crucial na indústria de processamento de borracha, influenciando diretamente a eficiência e a qualidade da produção. Com diversas opções disponíveis no mercado, escolher a rosca ideal pode ser um desafio. Neste artigo, abordaremos os diferentes tipos de roscas, fatores a considerar na escolha, suas vantagens e dicas de manutenção, ajudando você a tomar decisões informadas para otimizar sua produção.
Tipos de Roscas para Extrusoras de Borracha e Suas Aplicações
As roscas para extrusoras de borracha são componentes fundamentais que influenciam a eficiência e a qualidade do processo de extrusão. Existem diferentes tipos de roscas, cada uma projetada para atender a necessidades específicas de processamento de borracha. A escolha da rosca correta pode impactar diretamente a viscosidade, a temperatura e a homogeneidade do material durante a extrusão. A seguir, exploraremos os principais tipos de roscas e suas aplicações na indústria de borracha.
Um dos tipos mais comuns de roscas para extrusoras de borracha é a rosca de seção circular. Este tipo de rosca é amplamente utilizado devido à sua capacidade de gerar um fluxo uniforme do material. A seção circular permite uma distribuição homogênea da pressão e do calor, o que é essencial para a extrusão de borracha. Essa rosca é ideal para aplicações que exigem um processamento contínuo e eficiente, como na produção de perfis de borracha, mangueiras e outros produtos moldados.
Outro tipo importante é a rosca de seção trapezoidal. Este design é especialmente eficaz para materiais de alta viscosidade, pois proporciona uma maior capacidade de transporte do material. A rosca trapezoidal é frequentemente utilizada em processos que envolvem a mistura de aditivos e cargas na borracha, garantindo uma homogeneização adequada. Essa rosca é comumente aplicada na produção de compostos de borracha, onde a mistura uniforme de ingredientes é crucial para a qualidade do produto final.
As roscas de seção quadrada também têm seu lugar na indústria de extrusão de borracha. Este tipo de rosca é projetado para maximizar a área de contato entre a rosca e o material, o que resulta em uma maior eficiência de aquecimento e mistura. As roscas quadradas são frequentemente utilizadas em aplicações que exigem um controle preciso da temperatura e da viscosidade, como na produção de elastômeros e compostos de borracha especiais. A capacidade de controlar esses parâmetros é vital para garantir que o produto final atenda às especificações desejadas.
Além das seções mencionadas, as roscas podem ser classificadas de acordo com o seu passo. O passo da rosca refere-se à distância entre as voltas da rosca. Roscas de passo curto são ideais para materiais que requerem um maior tempo de residência, permitindo uma mistura mais completa e um aquecimento uniforme. Por outro lado, roscas de passo longo são mais adequadas para materiais que fluem facilmente, proporcionando uma extrusão mais rápida. A escolha do passo da rosca deve ser feita com base nas características do material a ser processado e nas exigências do produto final.
Outro aspecto a considerar é a configuração da rosca. As roscas podem ser simples ou compostas, dependendo da complexidade do processo de extrusão. Roscas compostas, que combinam diferentes seções e passos, são frequentemente utilizadas em aplicações que exigem uma mistura complexa de materiais. Por exemplo, na produção de borracha com propriedades específicas, como resistência ao calor ou à abrasão, uma rosca composta pode ser a melhor escolha para garantir que todos os componentes sejam adequadamente misturados e processados.
Além disso, a rosca pode ser projetada para incluir elementos de mistura, como lâminas ou elementos de corte. Esses elementos adicionais ajudam a melhorar a homogeneidade do material e a reduzir o tempo de processamento. A inclusão de elementos de mistura é especialmente útil em aplicações que envolvem a adição de cargas ou aditivos, pois garante que esses componentes sejam distribuídos uniformemente na matriz de borracha.
As roscas para extrusoras de borracha também podem ser adaptadas para atender a requisitos específicos de produção. Por exemplo, a utilização de um ANEL DE BLOQUEIO pode ser uma solução eficaz para evitar vazamentos de material durante o processo de extrusão. Este tipo de acessório é projetado para garantir que o material permaneça dentro da câmara de extrusão, melhorando a eficiência do processo e reduzindo o desperdício de material.
Em resumo, a escolha da rosca para extrusora de borracha deve ser feita com base nas características do material a ser processado e nas exigências do produto final. Compreender os diferentes tipos de roscas e suas aplicações é fundamental para otimizar o processo de extrusão e garantir a qualidade do produto. Ao considerar fatores como a seção da rosca, o passo e a configuração, os profissionais da indústria podem tomar decisões informadas que resultem em uma produção mais eficiente e de alta qualidade.
Fatores a Considerar na Escolha da Rosca para Extrusora de Borracha
A escolha da rosca para extrusora de borracha é um passo crucial que pode impactar significativamente a eficiência e a qualidade do processo de extrusão. Existem diversos fatores que devem ser considerados para garantir que a rosca selecionada atenda às necessidades específicas de produção. A seguir, discutiremos os principais aspectos a serem levados em conta ao escolher a rosca ideal para sua extrusora de borracha.
Um dos primeiros fatores a considerar é o tipo de material que será processado. A viscosidade, a temperatura de fusão e as propriedades reológicas do material influenciam diretamente a escolha da rosca. Materiais de alta viscosidade, por exemplo, podem exigir roscas com um design específico que permita um melhor transporte e mistura do material. Por outro lado, materiais que fluem facilmente podem ser processados com roscas de passo mais longo, que proporcionam uma extrusão mais rápida. Portanto, é fundamental entender as características do material antes de tomar uma decisão.
Outro aspecto importante é a geometria da rosca. As roscas podem ter diferentes seções transversais, como circular, trapezoidal ou quadrada, e cada uma delas oferece vantagens específicas. A seção circular, por exemplo, é ideal para um fluxo uniforme, enquanto a seção trapezoidal é mais adequada para materiais de alta viscosidade. A escolha da geometria deve ser feita com base nas exigências do processo e nas propriedades do material a ser processado.
Além da geometria, o passo da rosca também desempenha um papel crucial na escolha. O passo refere-se à distância entre as voltas da rosca e pode influenciar a eficiência do transporte do material. Roscas de passo curto são mais adequadas para materiais que requerem um maior tempo de residência, permitindo uma mistura mais completa. Em contrapartida, roscas de passo longo são mais indicadas para materiais que fluem facilmente, proporcionando uma extrusão mais rápida. A escolha do passo deve ser feita com base nas características do material e nas necessidades do produto final.
A temperatura de processamento é outro fator a ser considerado. A rosca deve ser capaz de suportar as temperaturas necessárias para o processamento do material sem comprometer sua integridade. Materiais que requerem temperaturas elevadas podem exigir roscas feitas de materiais especiais ou com revestimentos que aumentem a resistência ao calor. Além disso, a capacidade de controle da temperatura durante o processo de extrusão é fundamental para garantir a qualidade do produto final.
Outro ponto a ser avaliado é a configuração da rosca. Roscas simples podem ser suficientes para processos menos complexos, enquanto roscas compostas, que combinam diferentes seções e passos, são mais adequadas para aplicações que exigem uma mistura complexa de materiais. A configuração da rosca deve ser escolhida com base nas exigências do processo e nas características do material a ser processado.
A manutenção e a durabilidade da rosca também são fatores importantes a serem considerados. Roscas que exigem manutenção frequente podem aumentar os custos operacionais e o tempo de inatividade da máquina. Portanto, é recomendável optar por roscas que sejam projetadas para oferecer maior durabilidade e que exijam menos manutenção. Além disso, a facilidade de acesso para manutenção e reparos deve ser levada em conta ao escolher a rosca.
Outro aspecto relevante é a compatibilidade da rosca com o canhão da extrusora. A rosca deve ser projetada para se encaixar perfeitamente no canhão, garantindo um funcionamento eficiente e evitando vazamentos de material. A escolha de um canhão e rosca para injetora que sejam compatíveis é essencial para otimizar o processo de extrusão e garantir a qualidade do produto final.
Além disso, a capacidade de personalização da rosca é um fator a ser considerado. Em muitos casos, pode ser necessário adaptar a rosca para atender a requisitos específicos de produção. A possibilidade de personalizar a rosca, seja em termos de geometria, passo ou elementos de mistura, pode ser um diferencial importante para atender às necessidades do processo de extrusão.
Por fim, o custo da rosca também deve ser avaliado. Embora seja tentador optar pela opção mais barata, é fundamental considerar o custo total de propriedade, que inclui não apenas o preço de aquisição, mas também os custos de manutenção, operação e possíveis substituições. Investir em uma rosca de qualidade pode resultar em economia a longo prazo, devido à sua durabilidade e eficiência.
Em resumo, a escolha da rosca para extrusora de borracha envolve a consideração de diversos fatores, incluindo o tipo de material, a geometria da rosca, o passo, a temperatura de processamento, a configuração, a manutenção, a compatibilidade com o canhão, a personalização e o custo. Avaliar cuidadosamente esses aspectos garantirá que a rosca selecionada atenda às necessidades específicas de produção, resultando em um processo de extrusão mais eficiente e de alta qualidade.
Vantagens de Utilizar a Rosca Adequada na Produção de Borracha
A escolha da rosca adequada na produção de borracha é um fator determinante para a eficiência e a qualidade do processo de extrusão. A rosca desempenha um papel crucial na mistura, transporte e homogeneização do material, e sua seleção pode trazer diversas vantagens para a produção. Neste artigo, discutiremos as principais vantagens de utilizar a rosca correta na produção de borracha, destacando como isso pode impactar positivamente a operação e o produto final.
Uma das principais vantagens de utilizar a rosca adequada é a melhoria na eficiência do processo de extrusão. Roscas projetadas especificamente para o tipo de material a ser processado garantem um transporte mais eficiente, reduzindo o tempo de residência do material na extrusora. Isso resulta em uma produção mais rápida e em menor consumo de energia, o que é essencial para aumentar a competitividade no mercado. A eficiência do processo também se traduz em menores custos operacionais, permitindo que as empresas maximizem seus lucros.
Além da eficiência, a rosca correta também contribui para a homogeneidade do material. A mistura adequada dos componentes da borracha é fundamental para garantir que o produto final atenda às especificações desejadas. Roscas com design apropriado, como aquelas que incorporam elementos de mistura, ajudam a garantir que todos os aditivos e cargas sejam distribuídos uniformemente na matriz de borracha. Isso resulta em um produto final de alta qualidade, com propriedades consistentes e previsíveis.
A temperatura de processamento é outro aspecto que pode ser otimizado com a escolha da rosca adequada. Roscas projetadas para dissipar o calor de maneira eficiente ajudam a manter a temperatura do material dentro da faixa ideal durante o processo de extrusão. Isso é especialmente importante para materiais sensíveis ao calor, que podem sofrer degradação se expostos a temperaturas excessivas. Ao controlar a temperatura de forma eficaz, as empresas podem garantir que a qualidade do produto final não seja comprometida.
Outro benefício significativo da rosca adequada é a redução do desgaste e da manutenção do equipamento. Roscas de alta qualidade, projetadas para suportar as condições específicas do processo de extrusão, tendem a ter uma vida útil mais longa. Isso significa que as empresas podem reduzir os custos associados à manutenção e substituição de peças, resultando em uma operação mais econômica. Além disso, a facilidade de manutenção das roscas também é um fator a ser considerado, pois roscas que exigem menos intervenções são mais vantajosas para a operação.
A flexibilidade na produção é outra vantagem importante. A utilização de roscas que podem ser adaptadas para diferentes tipos de materiais e processos permite que as empresas respondam rapidamente às mudanças nas demandas do mercado. Isso é especialmente relevante em um ambiente de negócios dinâmico, onde a capacidade de se adaptar a novas exigências pode ser um diferencial competitivo. A possibilidade de personalizar a rosca para atender a requisitos específicos de produção também é um fator que pode agregar valor ao processo.
Além disso, a utilização da rosca adequada pode contribuir para a sustentabilidade do processo de produção. Roscas que otimizam o consumo de energia e reduzem o desperdício de material ajudam as empresas a operar de maneira mais sustentável. A eficiência energética é uma preocupação crescente na indústria, e a escolha de roscas que minimizam o impacto ambiental pode ser um diferencial importante para as empresas que buscam se posicionar como responsáveis socialmente.
Outro aspecto a ser considerado é a qualidade do produto final. A utilização da rosca correta não apenas melhora a eficiência do processo, mas também garante que o produto atenda aos padrões de qualidade exigidos pelo mercado. Isso é especialmente importante em setores onde a qualidade da borracha é crítica, como na fabricação de pneus, produtos médicos e componentes automotivos. A consistência e a confiabilidade do produto final são fundamentais para a satisfação do cliente e para a reputação da empresa.
Por fim, a integração da rosca com outros componentes do sistema de extrusão, como o Usinagem de Cilindros , pode maximizar ainda mais os benefícios do processo. A sinergia entre a rosca e o canhão da extrusora, por exemplo, é essencial para garantir um funcionamento suave e eficiente. A escolha de componentes que trabalhem em harmonia pode resultar em uma operação mais eficaz e em um produto final de qualidade superior.
Em resumo, a utilização da rosca adequada na produção de borracha oferece uma série de vantagens, incluindo melhoria na eficiência do processo, homogeneidade do material, controle da temperatura, redução do desgaste e manutenção, flexibilidade na produção, sustentabilidade, qualidade do produto final e integração com outros componentes do sistema. Ao considerar esses fatores, as empresas podem otimizar seu processo de extrusão e garantir que seus produtos atendam às expectativas do mercado, resultando em uma operação mais competitiva e lucrativa.
Manutenção e Cuidados com a Rosca para Extrusora de Borracha
A manutenção adequada da rosca para extrusora de borracha é essencial para garantir a eficiência e a durabilidade do equipamento. A rosca é um componente crítico no processo de extrusão, e sua integridade afeta diretamente a qualidade do produto final. Neste artigo, abordaremos as melhores práticas de manutenção e cuidados que devem ser adotados para prolongar a vida útil da rosca e otimizar o desempenho da extrusora.
Um dos primeiros passos na manutenção da rosca é a realização de inspeções regulares. Essas inspeções devem incluir a verificação visual da rosca e de seus componentes, buscando sinais de desgaste, corrosão ou danos. É importante observar se há rachaduras, deformações ou outros problemas que possam comprometer o funcionamento da rosca. A detecção precoce de problemas pode evitar falhas maiores e custos de reparo mais elevados no futuro.
A lubrificação é outro aspecto crucial na manutenção da rosca. A falta de lubrificação adequada pode levar ao aumento do atrito e ao desgaste prematuro do componente. É recomendável utilizar lubrificantes apropriados, conforme as especificações do fabricante, e aplicar a lubrificação nos pontos indicados. A frequência da lubrificação pode variar de acordo com a intensidade de uso da extrusora, mas, em geral, uma lubrificação a cada seis meses é uma boa prática. Em ambientes de trabalho mais exigentes, pode ser necessário aumentar a frequência.
Além da lubrificação, a limpeza da rosca e de seus componentes é fundamental. Resíduos de borracha, poeira e outros contaminantes podem se acumular ao longo do tempo, afetando o desempenho da extrusora. A limpeza deve ser realizada com produtos adequados que não danifiquem a superfície da rosca. É importante evitar o uso de solventes agressivos que possam causar corrosão ou desgaste. A limpeza regular ajuda a manter a eficiência do processo de extrusão e a qualidade do produto final.
Outro cuidado importante é a verificação das condições de operação da extrusora. A temperatura e a pressão devem ser monitoradas constantemente, pois condições inadequadas podem causar danos à rosca. A rosca deve ser projetada para suportar as temperaturas e pressões específicas do material a ser processado. Caso a extrusora opere fora das especificações recomendadas, isso pode resultar em falhas na rosca e na necessidade de substituição. Portanto, é essencial seguir as orientações do fabricante em relação às condições de operação.
A calibração da extrusora também é um aspecto que não deve ser negligenciado. A rosca deve estar corretamente alinhada com o canhão da extrusora para garantir um funcionamento suave. Um desalinhamento pode causar desgaste irregular e comprometer a eficiência do processo. A verificação do alinhamento deve ser realizada periodicamente, e ajustes devem ser feitos sempre que necessário. Isso não apenas prolonga a vida útil da rosca, mas também melhora a qualidade do produto final.
Além disso, a utilização de componentes de qualidade é fundamental para a manutenção da rosca. Investir em roscas e canhões de alta qualidade pode resultar em uma operação mais eficiente e em menor necessidade de manutenção. Componentes de baixa qualidade podem levar a falhas frequentes e custos elevados com reparos. Portanto, ao adquirir novos componentes, é importante optar por fornecedores confiáveis que ofereçam produtos com garantia e suporte técnico.
Outro ponto a ser considerado é a formação e capacitação da equipe responsável pela operação e manutenção da extrusora. Profissionais bem treinados são capazes de identificar problemas precocemente e realizar manutenções corretivas e preventivas de forma eficaz. A capacitação da equipe também inclui o conhecimento sobre as especificações do fabricante e as melhores práticas de operação, o que contribui para a longevidade do equipamento.
Por fim, a documentação das manutenções realizadas é uma prática recomendada. Manter um registro detalhado das inspeções, lubrificações, limpezas e quaisquer reparos realizados na rosca ajuda a identificar padrões de desgaste e a planejar manutenções futuras. Essa documentação pode ser útil para a tomada de decisões sobre a substituição de componentes e para garantir que a extrusora opere de maneira eficiente ao longo do tempo.
Em resumo, a manutenção e os cuidados com a rosca para extrusora de borracha são essenciais para garantir a eficiência e a durabilidade do equipamento. Inspeções regulares, lubrificação adequada, limpeza, monitoramento das condições de operação, calibração, utilização de componentes de qualidade, capacitação da equipe e documentação das manutenções são práticas que contribuem para a longevidade da rosca. Ao seguir essas diretrizes, as empresas podem otimizar seu processo de extrusão e garantir a qualidade do produto final, resultando em uma operação mais competitiva e lucrativa. Para serviços de qualidade, considere a Usinagem em americana sp que oferece soluções eficientes para suas necessidades de usinagem.
Em conclusão, a escolha e a manutenção adequadas da rosca para extrusora de borracha são fundamentais para garantir a eficiência e a qualidade do processo de produção. Compreender os diferentes tipos de roscas, os fatores que influenciam sua seleção e as práticas de manutenção necessárias permite que as empresas otimizem suas operações e melhorem a qualidade dos produtos finais. Investir em uma rosca adequada e seguir as diretrizes de manutenção não apenas prolonga a vida útil do equipamento, mas também resulta em uma produção mais eficiente e econômica. Ao tomar decisões informadas, você estará melhor preparado para enfrentar os desafios da indústria de processamento de borracha e alcançar resultados superiores.