Rosca para Injetora de Plástico: O Que Saber
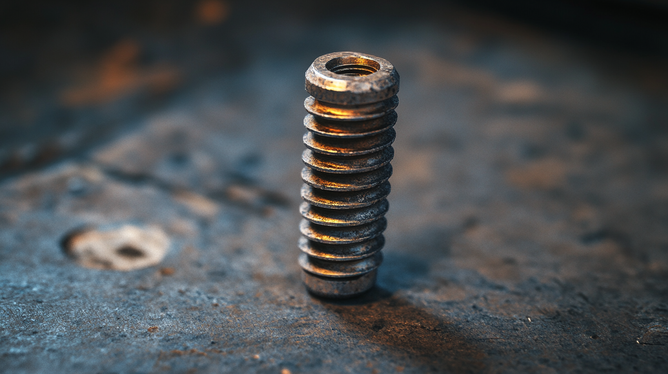
Por: João - 07 de Dezembro de 2024
A rosca para injetora de plástico é um componente essencial no processo de injeção, influenciando diretamente a qualidade do produto final. Neste artigo, iremos explorar o que é a rosca, os diferentes tipos disponíveis, dicas para escolher a ideal e as vantagens que ela pode trazer para sua produção. Continue lendo e descubra como esse elemento-chave pode otimizar suas operações e resultados.
O que é a Rosca para Injetora de Plástico
A rosca para injetora de plástico é um componente crucial no processo de moldagem por injeção, um método amplamente utilizado na indústria plástica para a produção de peças e produtos variados. Este elemento desempenha um papel fundamental na alimentação e na homogeneização do material plástico, garantindo que ele seja fundido e injetado de forma eficiente no molde.
Por definição, a rosca é uma estrutura cilíndrica com um perfil helicoidal que gira dentro do cilindro da injetora. Sua principal função é transportar o polímero do funil de alimentação até a câmara de injeção, onde o material é aquecido e derretido. Durante esse processo, a rosca também promove a mistura do material, resultando em uma consistência homogênea que é vital para a qualidade do produto final.
As roscas são projetadas considerando vários fatores, como o tipo de material a ser processado, a viscosidade do polímero, a temperatura de processamento e a forma do molde. A geometria da rosca, incluindo o seu comprimento, diâmetro e perfil, influencia diretamente no desempenho da injetora e na qualidade das peças produzidas. Portanto, a escolha da rosca adequada é essencial para otimizar a eficiência do processo de injeção.
Funcionamento da Rosca para Injetora de Plástico
Para entender o funcionamento da rosca, é importante esclarecer como o processo de injeção ocorre. O material plástico, geralmente na forma de pellets ou grânulos, é alimentado na câmara da injetora através do funil. Assim que os pellets entram em contato com a rosca, ela começa a girar. Esse movimento exerce uma força contínua sobre o material, empurrando-o em direção à extremidade da rosca, onde o aquecimento do material ocorre.
A rosca é projetada com diferentes seções que desempenham funções específicas:
- Seção de alimentação: Nesta área, os pellets são alimentados e começam a ser comprimidos. Este é o ponto onde a fricção e o calor começam a processar o material.
- Seção de compressão: Aqui, o material é ainda mais comprimido, aumentando sua temperatura e fluidificando-o para o próximo estágio do processo.
- Seção de medição: Neste segmento, o material já fundido é medido para garantir que a quantidade correta seja injetada no molde.
Essa sequência de operações garante que o material plástico seja aquecido, derretido e dosado corretamente antes de ser injetado no molde, onde assumirá a forma desejada.
Importância da Homogeneização
Um dos aspectos mais críticos da rosca para injetora de plástico é sua capacidade de homogeneizar o material. A homogeneização refere-se ao processo de misturar uniformemente todos os componentes do material plástico, incluindo aditivos e corantes, para garantir que o produto final tenha uma qualidade consistente.
Se a rosca não desempenhar adequadamente essa função, pode resultar em produtos com falhas, como manchas de cor, variações de espessura ou má adesão entre camadas. Portanto, roscas bem projetadas, que garantem uma mistura eficaz, são fundamentais para a produção de peças plásticas de alta qualidade.
Tipos de Rosca para Injetora de Plástico
Existem vários tipos de roscas projetadas para atender a diferentes necessidades de processamento de plástico. Entre os tipos mais comuns, destacam-se:
- Rosca padrão: É a configuração mais comum e é utilizada para uma ampla gama de polímeros.
- Rosca de alta compressão: Projetada para processar materiais de alta viscosidade, essa rosca possui um perfil que aumenta a compressão do material, facilitando seu derretimento.
- Rosca de baixa compressão: Indicada para materiais de baixa viscosidade, permitindo um transporte mais eficiente.
- Rosca especial: Projetadas para atender a requisitos específicos, como processamento de materiais com características particulares ou exigências de temperatura.
Fatores que Influenciam o Desempenho da Rosca
Vários fatores podem afetar o desempenho da rosca para injetora de plástico, e é essencial considerar cada um deles ao planejar a produção:
- Geometria da rosca: A forma e as dimensões da rosca devem ser escolhidas com cuidado para atender as especificações do material a ser processado.
- Velocidade de rotação: A velocidade da rosca influenciará a taxa de alimentação do plástico e a homogeneização do material.
- Temperatura de processamento: A temperatura deve ser ajustada de acordo com o tipo de plástico, impactando diretamente no processo de fusão e injeção.
- Pressão de injeção: A pressão aplicada durante a injeção é crucial para garantir que o plástico flua corretamente pelo molde.
Manutenção da Rosca para Injetora de Plástico
A manutenção adequada da rosca para injetora de plástico é fundamental para garantir sua durabilidade e desempenho. Isso inclui:
- Limpeza regular: O acúmulo de material pode afetar o desempenho da rosca, portanto, a limpeza frequente é essencial.
- Inspeção de desgastes: Verificar periodicamente se há desgaste nos elementos da rosca, como sulcos ou danos, é fundamental para evitar falhas.
- Ajuste de parâmetros de operação: Monitorar e ajustar os parâmetros de operação, como temperatura e pressão, garante uma operação estável.
Investir na manutenção da rosca pode prolongar sua vida útil e melhorar a eficiência do processo de injeção, resultando em produtos de maior qualidade.
Desafios e Soluções na Utilização da Rosca para Injetora de Plástico
Embora as roscas para injetoras de plástico desempenhem um papel crucial na produção, elas também podem apresentar desafios. Alguns dos principais problemas incluem:
- Degradação do material: Materiais plásticos sensíveis ao calor podem se degradar se expostos a temperaturas elevadas por muito tempo.
- Transporte inadequado: Se a geometria da rosca não for ideal, o material pode não ser transportado adequadamente, resultando em falhas no processo de injeção.
- Agrupamento de materiais: A mistura inadequada pode levar ao agrupamento de materiais, afetando a qualidade do produto final.
Para evitar esses problemas, é importante realizar testes e estudos sobre o material a ser processado e ajustar a rosca de acordo com as exigências de cada aplicação. Em muitos casos, a experiência e o conhecimento técnico podem fazer toda a diferença.
Conclusão da Seção
Em resumo, a rosca para injetora de plástico é um componente essencial no processo de moldagem por injeção, sendo responsável por transportar, aquecer e homogeneizar o material plástico. Sua geometria e design detém enorme importância na eficiência e qualidade do produto final. Ao entender seu funcionamento e a importância da escolha adequada e manutenção dessa peça, os profissionais do setor podem otimizar suas operações e garantir a produção de peças plásticas de alta qualidade. Ficar atento a inovações e práticas recomendadas neste campo também é fundamental para o sucesso das operações de injeção de plástico.
Tipos de Rosca para Injetora de Plástico
As roscas para injetoras de plástico são projetadas para atender a uma ampla variedade de necessidades de processamento de plástico, e cada tipo de rosca oferece características específicas que podem impactar diretamente a eficiência e a qualidade do produto final. Neste artigo, abordaremos os diversos tipos de roscas disponíveis, suas aplicações, características e as vantagens que cada uma pode proporcionar. Compreender esses tipos é crucial para otimizar os processos de injeção e escolher a rosca que melhor atende suas necessidades.
Rosca Padrão
A rosca padrão é a forma mais comum encontrada em injetoras de plástico. Ela é projetada para processar uma ampla gama de materiais plásticos, incluindo polipropileno (PP), polietileno (PE) e poliestireno (PS). Essa rosca é eficaz em padrões normais de moagem e mistura e conta com um design equilibrado que proporciona uma boa eficiência no processamento.
As características típicas da rosca padrão incluem:
- Geometria cilíndrica: Possui um perfil simples que permite um transporte eficaz do material.
- Comprimento proporcional: Geralmente, o comprimento da rosca é adequado para uma combinação razoável de compressão e medição do material.
- Versatilidade: Ideal para uma variedade de resinas e aditivos, facilitando o uso em diferentes aplicações.
Rosca de Alta Compressão
As roscas de alta compressão são projetadas para processar materiais plásticos que apresentam alta viscosidade ou que exigem um aumento significativo na pressão durante o processamento. Essas roscas são especialmente úteis ao trabalhar com materiais como poliuretano, que tendem a ser mais densos e difíceis de fundir.
Entre as características das roscas de alta compressão, destacam-se:
- Alta taxa de compressão: O design favorece a compressão do material em um espaço menor, resultando em maior pressão na câmara de injeção.
- Geometria específica: Com ranhuras profundas e uma configuração projetada para maximizar a mistura, a rosca garante uma fusão adequada do material.
- Temperaturas elevadas: Melhor capacidade de operar em temperaturas mais altas, ajudando na fusão de polímeros difíceis.
Rosca de Baixa Compressão
As roscas de baixa compressão são utilizadas para processar materiais de baixa viscosidade, permitindo que as resinas fluam com mais facilidade durante o processo de injeção. Esse tipo de rosca é vantajoso ao se trabalhar com plásticos como polietileno de baixa densidade (LDPE) e outros polímeros que não requerem uma alta pressão para fusão.
- Perfil de menor profundidade: O design da rosca apresenta ranhuras mais rasas, facilitando o fluxo do material.
- Redução na necessidade de pressão: Permite dados mínimos de pressão, preservando a integridade do material durante o processo.
- Eficiência energética: A operação da injetora requer menos energia para o processamento de polímeros mais fluidos.
Rosca Paralela
A rosca paralela é uma configuração mais avançada que apresenta duas ou mais roscas que operam em paralelo. Essa configuração é comum em injetoras de dupla rosca e é particularmente útil para aplicações que requerem uma mistura intensa de materiais ou a adição de aditivos específicos.
- Alta eficiência em mistura: O design permite uma mistura mais homogênea de diferentes resinas ou aditivos.
- Capacidade de processamento de compostos: Ideal para composições plásticas que exigem a fusão de múltiplos materiais simultaneamente.
- Versatilidade na produção: Pode ser adaptada para diferentes proporções de materiais, ampliando as opções de produção.
Rosca de Co-Extrusão
A rosca de co-extrusão é um tipo especializado que se destina a processar mais de um material simultaneamente. Essa configuração é frequentemente utilizada em aplicações que requerem camadas de diferentes polímeros, como filmes plásticos ou tubos multicamadas. A co-extrusão permite a criação de produtos com características distintas em cada camada.
- Fluidez controlada: Permite o controle da extrusão dos diferentes materiais, garantindo que sejam pedidas adequadamente nos moldes.
- Camada avançada: Possibilita a construção de produtos multicamadas com propriedades específicas, como resistência química ou barreira a gases.
- Eficiência em produção: Reduz o desperdício de material permitindo a incorporação de reciclados em novas formulações.
Rosca de Injeção e Reciclagem
Com a crescente demanda por práticas sustentáveis na indústria de plásticos, as roscas de injeção e reciclagem têm ganhado destaque. Essas roscas são projetadas para processar materiais plásticos reciclados, permitindo a reutilização eficiente de plásticos em novas produções. Essa modalidade de rosca apresenta um design que favorece a fusão e a mistura de plásticos com propriedades variadas.
- Compatibilidade com materiais reciclados: Projetada para lidar com as variações que os plásticos reciclados podem apresentar.
- Processamento em temperaturas adequadas: Permite que os materiais reciclados sejam fundidos sem degradar suas propriedades.
- Contribuição ambiental: Ajuda na redução do impacto ambiental ao permitir que plásticos sejam reutilizados em vez de descartados.
Fatores a Considerar na Escolha da Rosca
Ao selecionar a rosca adequada para sua injetora de plástico, considere os seguintes fatores:
- Tipo de material: A escolha deve ser baseada nas propriedades do plástico que será utilizado, como viscosidade e temperatura de fusão.
- Objetivo de produção: Defina o que deseja alcançar com o produto final e como a escolha da rosca pode afetar este resultado.
- Eficiência energética: Analise se a rosca escolhida proporciona economia de energia durante o processo de injeção.
- Manutenção e facilidade de operação: Roscas que exigem menos manutenção podem ser mais vantajosas a longo prazo.
Conclusão da Seção
Existem diversos tipos de roscas para injetoras de plástico, cada uma projetada para atender a necessidades específicas de processamento. Desde roscas padrão até configurações mais especializadas, a escolha da rosca certa é vital para garantir a eficiência do processo de injeção e a qualidade do produto final. Conhecer as características e aplicações de cada tipo de rosca facilita decisões informadas que podem melhorar tanto a produtividade quanto a sustentabilidade dos processos de produção na indústria plástica.
Como Escolher a Rosca Ideal para sua Injetora
A escolha da rosca ideal para sua injetora de plástico é um fator crucial para garantir a eficiência e a qualidade do processo de moldagem por injeção. Uma rosca bem escolhida pode influenciar diretamente na produtividade, na homogeneização do material e, consequentemente, na qualidade do produto final. Neste artigo, exploraremos os principais critérios a considerar ao selecionar a rosca adequada, as vantagens de uma escolha consciente e as implicações de uma decisão errada.
Entenda o Material a Ser Processado
O primeiro passo na escolha da rosca ideal é compreender as propriedades do material plástico que você pretende processar. Cada tipo de plástico possui características distintas que afetam sua fusão, viscosidade e processabilidade. Por isso, é fundamental conhecer:
- Tipo de Polímero: Diferentes plásticos, como polipropileno (PP), polietileno (PE) e poliéster, possuem variadas temperaturas de fusão e comportamentos de fluidez. Conhecer o tipo de polímero auxiliará a determinar a configuração da rosca mais adequada.
- Viscosidade: A viscosidade do material influencia a rosca escolhida. Materiais de alta viscosidade exigem roscas que ofereçam maior compressão e mistura, enquanto materiais de baixa viscosidade se beneficiam de roscas com baixa compressão.
- Temperatura de Processamento: Cada material requer uma temperatura específica para sua fusão. Portanto, é essencial que a rosca suporte as temperaturas necessárias sem comprometer suas propriedades.
Defina a Aplicação do Produto
Após entender o material, o próximo passo é definir a aplicação para a qual o produto final será destinado. Isso ajudará a determinar as exigências específicas que a rosca deve atender. Considere:
- Estrutura do Produto: Produtos que exigem alta resistência ou durabilidade podem demandar uma rosca que proporcione uma fusão mais homogênea e uma qualidade consistente.
- Exigências Estéticas: Se o produto final precisa apresentar uma cor específica ou textura, a rosca deve ser capaz de misturar aditivos e pigmentos de forma eficaz.
- Produção em Massa: Para produção em larga escala, considere roscas que maximizam a eficiência e suportam altas taxas de injeção sem comprometer a qualidade.
Considere a Geometria da Rosca
A geometria da rosca é um dos aspectos mais importantes a considerar na seleção da rosca ideal. A forma e o design da rosca afetam a eficiência do processo e a qualidade do material processado. Aqui estão alguns pontos a considerar:
- Comprimento e Diâmetro: Uma rosca longa e estreita pode ser ideal para materiais que exigem um maior tempo de aquecimento e mistura, enquanto roscas mais curtas e largas podem ser mais eficazes para materiais de baixa viscosidade.
- Perfil da Ranhura: O perfil e a profundidade das ranhuras influenciam a taxa de mistura e a compactação do material. Ranhuras mais profundas podem ser vantajosas para polímeros de alta viscosidade.
- Quantidade de Seções: Roscas com várias seções (como alimentação, compressão e medição) podem oferecer vantagens significativas em termos de eficiência de mistura.
Avalie a Capacidade de Homogeneização
A homogeneização do material é fundamental para garantir a qualidade do produto final. Ao escolher uma rosca, verifique se ela tem o design necessário para promover uma mistura adequada. É importante considerar:
- Mixagem Eficiente: Uma boa rosca deve promover a mistura de todos os componentes do material, garantido que aditivos, corantes e outros ingredientes sejam uniformemente dispersos.
- Redução de Variações: Se a rosca não homogeneizar bem, pode resultar em produtos com variações de cor e resistência, o que pode afetar a aceitação do mercado.
- Desempenho Consistente: Escolher uma rosca que propicie uma homogeneização eficaz ajudará a garantir que cada lote produzido atenda aos padrões de qualidade desejados.
Considere a Eficiência Energética
A eficiência energética é um fator cada vez mais importante na escolha do maquinário e dos componentes utilizados na produção. Algumas roscas podem consumir mais energia do que outras, impactando diretamente o custo operacional. Considere:
- Desperdício de Calor: Escolher roscas que mantenham melhor o calor ajuda na eficiência, reduzindo a quantidade de energia necessária para fundir o plástico.
- Eficiência de Processamento: A operação da rosca deve garantir um bom desempenho com o mínimo de consumo de energia, o que pode reduzir custos e apresentar vantagens competitivas.
- Uso de Materiais Reciclados: Se sua empresa utiliza materiais reciclados, escolher uma rosca projetada para o processamento de plásticos reciclados pode resultar em maior eficiência e menor consumo energético.
Analise a Manutenção Necessária
Outra consideração importante é a manutenção da rosca. Uma rosca que exige muita manutenção pode aumentar os custos operacionais e o tempo de inatividade da máquina. Pergunte-se:
- Acessibilidade: A rosca deve ser projetada para facilitar a manutenção. Modelos que exigem menos desmontagem são preferíveis.
- Duração da Peça: Verifique a durabilidade dos materiais da rosca e se eles podem resistir a desgastes comuns ao longo do tempo.
- Facilidade de Limpeza: Uma rosca que permite limpeza rápida e eficiente contribuirá para a manutenção da qualidade do material e reduzirá o tempo de inatividade.
Pense na Flexibilidade de Produção
A flexibilidade de uma rosca para processar diferentes tipos de materiais pode ser um aspecto valioso, especialmente se sua linha de produção lida com vários polímeros ou formulações. Considere:
- Capacidade de Ajuste: Roscas que podem ser ajustadas ou configuradas para diferentes tipos de polímeros oferecem uma ampla gama de aplicações.
- Compatibilidade com Vários Materiais: Escolher uma rosca que funcione com uma variedade de materiais é uma vantagem competitiva que pode facilitar a adaptação a novas demandas de mercado.
- Menor Tempo de Alteração: A flexibilidade no design da rosca pode reduzir o tempo necessário para alternar entre diferentes tipos de produção.
Colabore com Profissionais Especializados
Por fim, a colaboração com engenheiros de processos e especialistas em plásticos pode ser um fator decisivo na escolha da rosca ideal. Profissionais experientes possuem o conhecimento técnico necessário para:
- Identificar Necessidades Específicas: Podem ajudar a identificar requisitos específicos que sua produção pode demandar, considerando os fatores mencionados anteriormente.
- Realizar Testes e Simulações: Especialistas podem sugerir testes e simulações que ajudem a prever o desempenho da rosca em condições reais de operação.
- Oferecer Aconselhamento Continuado: Podem fornecer orientações contínuas sobre otimização e melhoramento dos processos, à medida que novos desafios surgem no ambiente de produção.
Conclusão da Seção
A escolha da rosca ideal para sua injetora de plástico envolve uma série de considerações fundamentais que impactam diretamente a eficiência, a qualidade e a lucratividade do seu processo de produção. Analisando cuidadosamente o material a ser processado, a aplicação desejada, a geometria da rosca, a homogeneização, a eficiência energética, a manutenção e a flexibilidade, você poderá tomar uma decisão informada e assertiva. Ao final, contar com a ajuda de especialistas pode fazer toda a diferença na implementação de soluções inovadoras e eficientes na sua operação, alinhando sua empresa às melhores práticas do setor.
Vantagens da Rosca para Injetora de Plástico
A rosca para injetora de plástico desempenha um papel fundamental no processo de moldagem por injeção, um método amplamente utilizado na indústria de plásticos. Essa peça essencial não apenas facilita a fusão e a injeção do material plástico, mas também traz uma série de vantagens que impactam diretamente a qualidade do produto final, a eficiência da produção e os custos operacionais. Neste artigo, exploraremos detalhadamente as principais vantagens da rosca para injetora de plástico, evidenciando sua importância para processos produtivos bem-sucedidos.
1. Eficiência no Processo de Produção
A rosca para injetora de plástico é projetada para otimizar a eficiência do processo de injeção. Com uma geometria adequada, ela transporta o material através da câmara de injeção de maneira eficiente, minimizando o tempo necessário para fundir e injetar o material. Essa eficiência se traduz em ciclos de produção mais rápidos, resultando em:
- Redução do Tempo de Ciclo: A rosca é responsável por aquecer e misturar o material rapidamente, permitindo um ciclo de produção mais curto.
- Aumento da Produtividade: Com ciclos mais rápidos, as empresas podem aumentar sua produção diária, atendendo melhor a demanda do mercado.
- Menor Consumo Energético: A eficiência da rosca ajuda a reduzir o consumo de energia, tornando o processo mais sustentável.
2. Qualidade do Produto Final
Um dos aspectos mais críticos na produção de plásticos é a qualidade do produto final. A rosca para injetora tem um impacto significativo nesta qualidade, pois desempenha um papel vital na homogeneização do material. Isso resulta em:
- Uniformidade na Mistura: A rosca promove uma mistura homogênea de aditivos, corantes e resinas, garantindo que o produto final tenha cores e propriedades consistentes.
- Melhoria na Resistência e Durabilidade: Um material bem fundido com aditivos adequadamente dispersos resulta em produtos com características mecânicas superiores, aumentando a resistência e a vida útil.
- Menor Taxa de Defeitos: A homogeneização adequada reduz a probabilidade de defeitos nos produtos, como de descoloração, bolhas ou falhas de adesão.
3. Versatilidade no Processamento
As roscas para injetoras de plástico são projetadas para serem versáteis, o que é uma enorme vantagem para as operações de produção. Essa versatilidade se reflete em vários aspectos:
- Capacidade de Processar Diferentes Materiais: A rosca pode ser adaptada para lidar com uma ampla variedade de polímeros, permitindo o processamento de materiais com diferentes propriedades.
- Adequação para Aplicações Diversificadas: Desde componentes automotivos até produtos médicos, a flexibilidade na escolha da rosca permite a fabricação de uma vasta gama de produtos.
- Facilidade de Ajuste e Personalização: Muitas roscas permitem ajustes de configuração e personalização para atender a requisitos específicos, o que amplia as opções de produção.
4. Custo-Benefício
A eficiência e a eficácia das roscas para injetoras também se traduzem em vantagens econômicas significativas para as empresas. Os benefícios econômicos incluem:
- Redução de Desperdícios: O uso otimizado dos materiais e a homogeneização reduz o desperdício durante o processo de produção, resultando em economia de custos.
- Menor Custo Operacional: Com um ciclo de produção mais rápido e eficiente, as empresas podem reduzir seus custos operacionais gerais.
- Retorno sobre o Investimento Melhora: Os ganhos em eficiência e produtividade contribuem para um retorno sobre o investimento mais rápido ao adquirir uma nova rosca ou injetora.
5. Confiabilidade e Durabilidade
As roscas para injetoras de plástico são projetadas para serem duráveis e confiáveis ao longo do tempo. Essa durabilidade traz várias vantagens:
- Menos Paradas para Manutenção: Roscas de qualidade exigem menos manutenção, reduzindo o tempo de inatividade da máquina e os custos associados.
- Maior Vida Útil: O investimento em roscas de bom desempenho resulta em uma vida útil prolongada, diminuindo a necessidade de substituições regulares.
- Desempenho Estável: A confiabilidade das roscas assegura um desempenho consistente ao longo do tempo, resultando em ciclos de produção previsíveis e controláveis.
6. Consistência na Produção
A produção estável e consistente é vital para a indústria de plásticos. A rosca para injetora contribui para que esse objetivo seja alcançado de várias maneiras:
- Controle de Temperatura: As roscas modernas são projetadas para manter um controle constante da temperatura durante a fusão do material, garantindo que a qualidade do produto não seja comprometida.
- Taxa de Feed Constante: A rosca assegura uma taxa de alimentação contínua e controlada dos pellets ou grânulos, mantendo a uniformidade no processo.
- Minimização de Variações: A capacidade da rosca de manter a inseta adequada de temperatura e pressão resulta em variações mínimas no produto final, assegurando consistência em cada lote produzido.
7. Capacidade de Integração com Tecnologias Avançadas
As roscas para injetoras de plástico podem ser integradas a tecnologias modernas, como automação, sensoriamento e monitoramento em tempo real. A capacidade de integrar tecnologia traz benefícios adicionais:
- Monitoramento em Tempo Real: Sensores podem ser utilizados para monitorar a temperatura e a pressão na câmara de injeção, permitindo ajustes imediatos para otimização do processo.
- Aumento da Automação: A integração com sistemas automatizados de produção reduz a necessidade de intervenção humana, aumentando ainda mais a eficiência e a precisão do processo.
- Data Collection: A capacidade de coleta de dados ao longo do processo ajuda na análise de desempenho e na identificação de oportunidades de melhoria contínua.
8. Sustentabilidade e Eficiência Energética
Com a crescente preocupação com a sustentabilidade ambiental, a eficiência energética da rosca para injetora é um ponto positivo a se considerar. As vantagens relacionadas à sustentabilidade incluem:
- Redução do Consumo de Energia: Roscas eficientes ajudam a reduzir o consumo energético, resultando em uma pegada de carbono menor.
- Processamento de Materiais Reciclados: Muitas roscas são projetadas para processar plásticos reciclados, contribuindo para uma prática mais sustentável na produção de plásticos.
- Menor Geração de Resíduos: Ao otimizar o uso de materiais e minimizar desperdícios, as roscas contribuem para a geração reduzida de resíduos plásticos.
9. Melhoria na Segurança do Processo
A segurança é uma consideração crucial em qualquer ambiente de produção. As roscas para injetoras de plástico podem contribuir para a segurança operacional de diversas formas:
- Funcionamento Suave: Uma rosca de alta qualidade garante um funcionamento suave e uniforme, minimizando o risco de falhas mecânicas.
- Minimização de Interferências: Roscas bem projetadas diminuem o risco de entupimentos ou bloqueios, que podem levar a situações perigosas durante a operação.
- Controle de Temperatura: A manutenção de temperaturas adequadas reduz o risco de superaquecimento e possíveis acidentes relacionados.
10. Suporte e Assistência Técnica
Finalmente, ao investir em uma rosca para injetora de plástico, as empresas frequentemente se beneficiam do suporte e assistência técnica oferecidos pelos fabricantes. Esse suporte é valioso em várias situações:
- Treinamento de Operadores: Os fabricantes costumam oferecer treinamentos para operadores, assegurando que eles possam utilizar e manter a rosca corretamente.
- Apoio na Resolução de Problemas: Em caso de dificuldades operacionais, o suporte técnico pode ser crucial para resolver questões rapidamente.
- Atualizações e Melhorias: A assistência técnica possibilita a realização de melhorias e atualizações no equipamento, mantendo a operação competitiva e atualizada.
Conclusão da Seção
As vantagens da rosca para injetora de plástico são amplas e impactam diversos aspectos do processo de moldagem por injeção. Desde a eficiência na produção até a qualidade do produto final, a escolha correta da rosca é fundamental para o sucesso das operações industriais. Com a capacidade de oferecer flexibilidade, custo-benefício, confiabilidade e integração com tecnologias avançadas, a rosca é um investimento essencial para qualquer empresa que busca otimizar sua linha de produção e atender às demandas do mercado de forma sustentável e eficiente.
Em resumo, a rosca para injetora de plástico é um componente vital que desempenha um papel crucial em todo o processo de moldagem por injeção. Desde a sua função primordial de transportar e homogeneizar o material até influenciar diretamente a qualidade e eficiência do produto final, a rosca não pode ser subestimada. A escolha do tipo correto de rosca, bem como a consideração de fatores como geometria, capacidade de homogeneização e eficiência energética, pode resultar em significativas melhorias na produtividade e na redução de custos operacionais. Além disso, ao optar por uma rosca que atenda às demandas específicas do seu processo e produto, você estará não apenas atendendo às necessidades atuais, mas também se preparando para um futuro sustentável e inovador na indústria plástica. Portanto, invista tempo na análise e na escolha da rosca ideal; essa decisão pode ser a chave para otimizar suas operações e alcançar resultados excepcionais.